
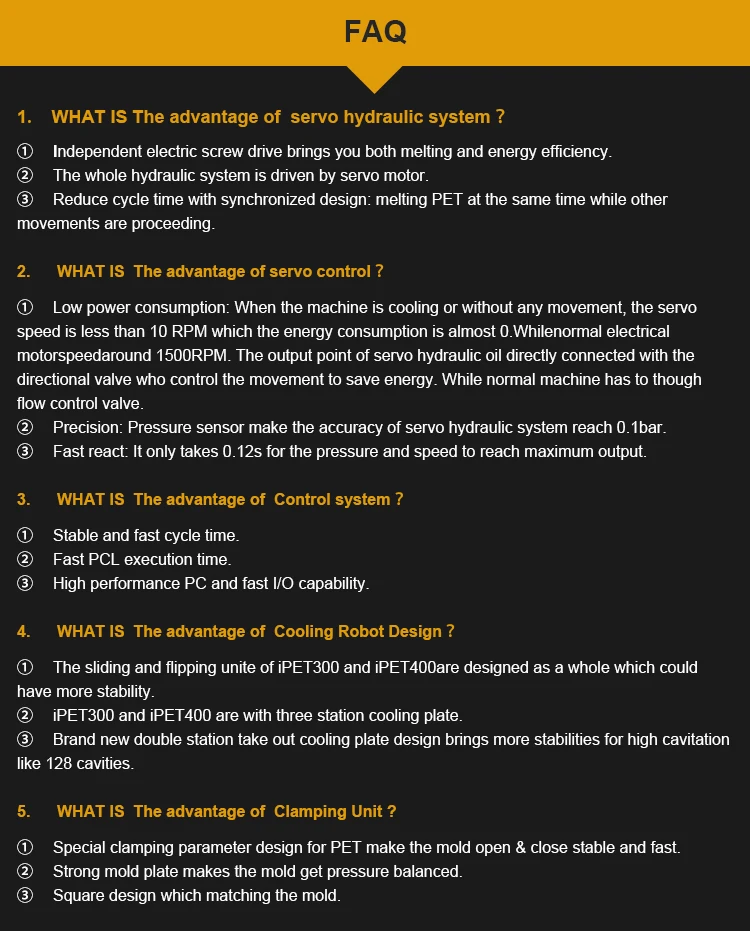
The design criteria in this guide may not apply to parts molded from some engineering resins. Most require drying before processing, specially designed extruder screws and specific processing conditions. These resins require special consideration prior to molding. Some of the acronyms include PPO, PC, PETG, ABS, TPE – you get the idea. Many engineering-grade resins can be blow molded. These materials usually form parts matching the principles discussed in this design guide.
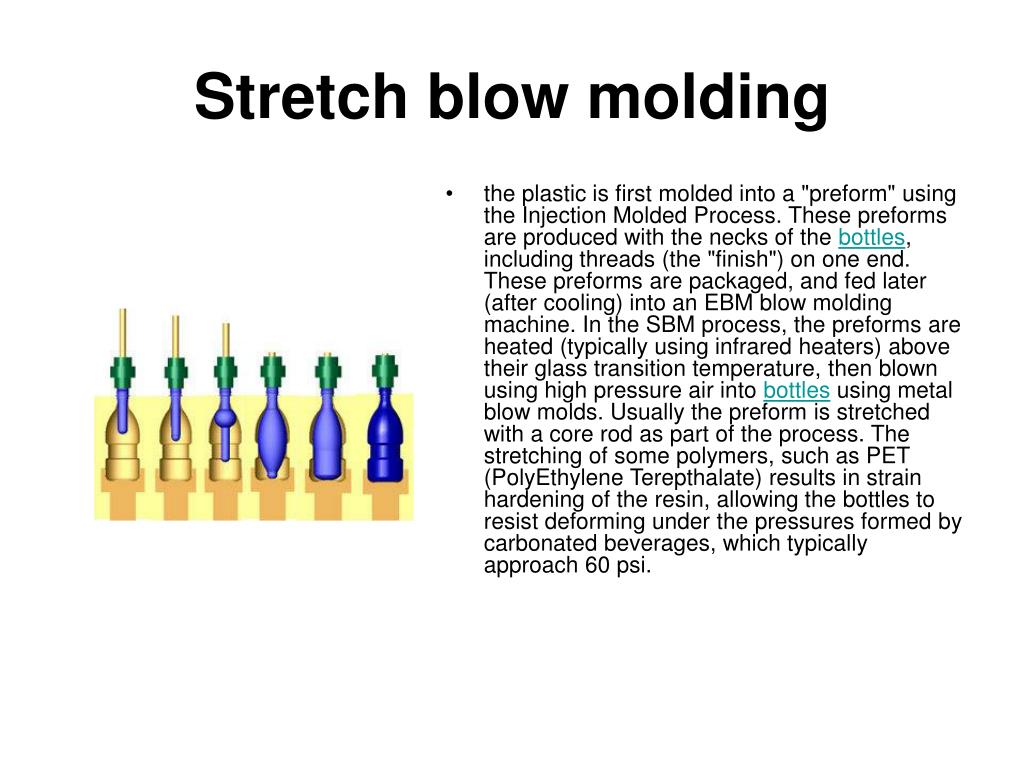
One difference is temperature performance with PE performing better at -75 to +160 degrees F and PP performing well from -0 to +170 degrees F. These materials are resistant to most chemicals. PE is currently less expensive but PP tends to be stiffer which sometimes offsets the cost difference. Polyethylene (PE) and polypropylene (PP) are the most popular blow molding resins. Some of the least expensive materials are also the easiest to process. Experience with blow molding grade materials is essential and we have practical molding experience using every blow moldable material Commodity Materials Material selection is a critical aspect of design and should involve serious study of:Īlthough there are thousands of plastic materials available, most won’t meet the needs of your product. (Most finishing steps can be completed in-mold but some involve secondary operations.)
#PREFORM BLOW MOLDING SOFTWARE#
Software products can help predict molding characteristics and our engineers are here to help make your product great. This guide focuses on the extrusion blow molding process. No two designs are alike, so the mold and process must be adjusted to optimize each design. The Custom-Pak blow molding design guide provides you with basic design tools for making engineered blow molded parts.
